
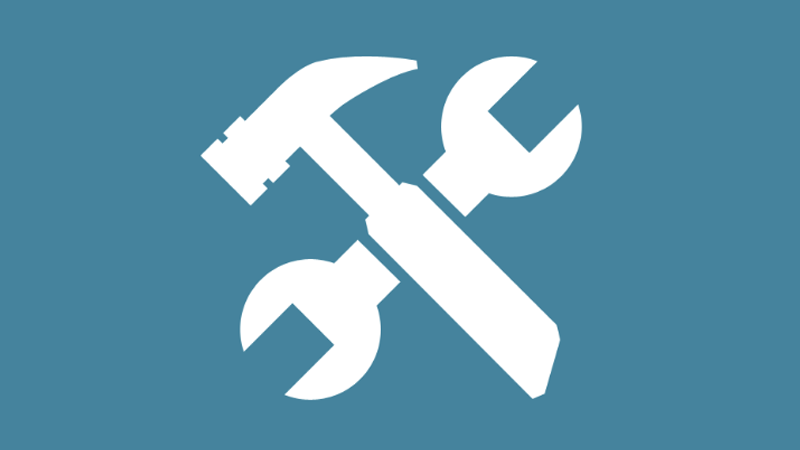
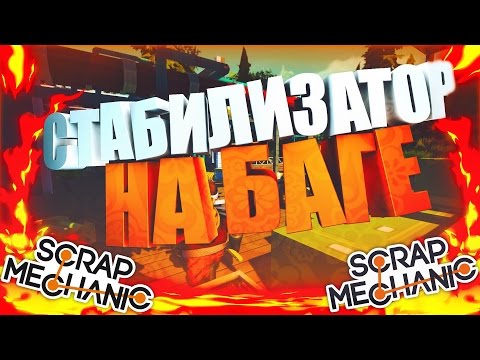
Any and all product data handed over to your CM must be current and correct so he or she can build to spec failing to do so is a major cause of rework and scrap. You may need to provide the CM with a manufacturing build package, like a PDX file, which contains product data including CAD drawings, datasheets, work instructions, BOM records, and change details. If you are outsourcing manufacturing activities to a third-party like a contract manufacturer (CM), product documentation becomes even more important. Incorrect BOM information can result in ordering the wrong parts-and if the parts can’t be returned or used in other products, they become scrap for the company. Because so many business decisions, like part-ordering, can be driven from a BOM, it is crucial that the information contained within a BOM is accurate and up-to-date. In addition to product drawings, it is important that manufacturers create and maintain a BOM for each product. While CAD drawings are a vital part of documenting product information, they fail to capture complex bill of materials (BOM) information or show changes made to a design once it moves into production, so relying exclusively on CAD drawings increases the odds of error and makes scrap and rework more likely to occur. However, this couldn’t be further from the truth. Many small to mid-sized manufacturers believe their documentation bases are covered if they’re capturing designs in a CAD tool. If priority is given to evaluating and improving your manufacturing processes, it becomes much easier to reduce the amount of scrap and rework in your organization. And while no one, especially an operations manager, wants to admit it, these expenses add up quickly and negatively impact the bottom line.Īlthough it is near-impossible to eliminate scrap and rework completely, you can reduce the amount of scrap and rework in your organization by optimizing the way you document product data, review manufacturing processes, and communicate manufacturing and engineering changes throughout your supply chain. Scrap and rework costs are caused by many things-when the wrong parts are ordered, when engineering changes aren’t effectively communicated or when designs aren’t properly executed on the manufacturing line.No matter why scrap and rework occurs, its impact on an organization is always the same-wasted time and money. Scrap and rework costs are a manufacturing reality impacting organizations across all industries and product lines.
